Black flotation machine is suitable for non-ferrous metal sorting, but also for non-metallic such as: coal fluorite, talc sorting. The flotation machine drives the impeller to rotate by the motor triangle generation, and generates centrifugal force to form a negative pressure. On the one hand, the air is mixed with the slurry, and on the other hand, the slurry is mixed with the medicine, and the foam is refined to make the mineral bond foam. , floating to the pulp surface to form mineralized foam. Adjust the height of the shutter and control the liquid level so that the useful foam is scraped off by the scraper.
The flotation machine is the most commonly used method for beneficiation . Generally, the material is crushed to the separation degree of the crystal body by the crusher ball mill and other equipment, and then selected by a flotation machine and the like.
What problems should be paid attention to when using and maintaining the flotation machine:
1. The working capacity and working period of the flotation machine are the same as those of other machines. The maintenance and maintenance of the main parts are normal. All the working parts should be carefully checked in 3-4 months, and the new flotation Regular inspections of the machine for the first few months of work;
2. Only qualified personnel can carry out inspections;
3. In order to replace the wearing parts in time to shorten the downtime, it is necessary to regularly reserve a full set of wearing parts in the warehouse to determine the date of use and the organization such as reserve amount according to the specific conditions.
4, must ensure that the operator of the flotation machine has a certain technical know or training to force him to fully understand the machine.
5. In order to avoid the mixing of waste and useless materials into the oil, there should be a filter when filling the oil. When the flotation machine is working, the oil cover should be sealed.
6, after driving to check, and contact with the upper and lower process can be started.
7. The order of driving is: press the upper switch and press the start button.
8. After driving, strictly touch the rotating part with your hand.
Bearing type: Good-quality bearings, sealed and protected from dirt and water, are the key to long and healthy hubs. Older or less expensive hubs may use cup and cone bearings, which contains two rings of loose ball bearings that sit in 'cups 'inside the hub body, and are secured in place by conical nuts known as' cones'. The balls can rotate freely between the cup and cone with each unit making up one bearing.
Cup and cone bearings have the advantage of being easily serviced at home – new bearings and a dollop of grease once in a while are all you need to keep them running smoothly – but they can be tricky to adjust perfectly. More expensive hubs may use cartridge bearings , where the steel balls or needles rotate in a single cartridge unit that can be easily removed for servicing or replaced once worn out. Many riders prefer the convenience of cartridge bearings – no more tedious micro-adjusting or hunting for stray ball bearings mid- service – but they are more expensive to replace.
• Materials: Most MTB hubs, front and rear, will be made of lightweight aluminium alloy although carbon fibre units are available at the top end of the market. Rear hubs for trail, jump and gravity bikes may use steel rather than aluminium freewheels to prevent the softer alloy splines being chewed up by the cassette under heavy load.
• Brake rotor compatibility: Bikes running disc brake systems need hubs to which the disc rotor can attach. There are two main standards for rotor mounting, six-bolt and Centrelock . As the name suggests, six-bolt systems have hubs with six evenly- spaced holes to bolt on a matching rotor. Rotor bolts generally use Torx heads so you will need to make sure you have a Torx tool to tighten or loosen them – don't try to fudge the job with an Allen key or you will risk stripping the bolts.
The Centrelock system used by Shimano foregoes rotor bolts in favour of a splined hub-rotor interface secured with a locking ring (special tool needed). This is claimed to reduce installation time but it does put limits on mixing and matching hubs and brakes as most other manufacturers stick with the six-bolt system. Again however, adaptors are available to mount six-bolt rotors to Centrelock hubs, and vice-versa. Before investing in new hubs check which disc interface you are currently using and buy accordingly.
• Axle size (front): You must also ensure that your hubs are compatible with your fork axle. Many entry-level or shorter-travel cross-country forks attach to the hubs via quick-release (QR) skewers, with a 9mm diameter axle clamped into the fork and frame dropouts via a 5mm QR skewer. However recent years have seen the growth of the 'bolt-through' or 'thru-axle' standard on MTB front forks for trail, enduro and gravity riders. This uses a larger-diameter (12mm, 15mm or 20mm) axle for extra stiffness and security, with the axle threading right through the fork ends and being secured by two QR clamps integrated into the fork lowers.
If you intend to upgrade your wheels make sure the hubs match whichever axle standard you are using, or alternate consider hubs that can switch between QR and bolt-through with the insertion of a simple adaptor to enable the wheels to be used with different fork types .
• Axle size (rear): Rear hubs are sized according to the diameter and length of the rear axle (measured in millimetres). The standard MTB rear axle dimensions are 135x5mm (for a QR rear hub) but jump and gravity bikes may use wider and thick axles for extra strength and stiffness, with the available sizes being 135 × 10, 142 × 12, 150 × 12, 157 × 12 and 165 × 12. Ensure your rear hub is the correct size to fit your frame.
• Rims: If choosing a new hub to rebuild a wheelset you will need to match the number and type of spoke holes on the hub's flange to the number and type of spoke holds drilled into the rim, eg a 32h hub is designed for a 32 -spoke wheel, and needs to be matched to a 32h rim.
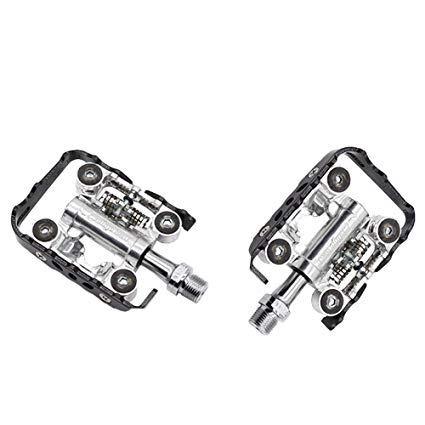
Bicycle Pedals,Aluminum Bicycle Pedal,Aluminum Mold Bicycle Pedal,Aluminum Die Casting Bicycle Pedal
Ningbo Jinyao Machinery Company. LTD , https://www.cardiecastingmold.com