Abstract: This paper first briefly introduces the two characteristics of the new four-valve pulse tube refrigerator compared with the ordinary four-valve pulse tube refrigerator. The first one is that "L" type vascular structure replaces the usual "I" type Vascular structure greatly simplifies the structure of the cold end of the vessel and improves the symmetry of the structure of the chiller. The horizontal part of the vessel can be co-cooled with the cold head. The second is the use of a double orifice valve structure instead of the usual Single-orifice valve structure, used to control the quality of the hot end of the gas flow into the exhaust. Then the preliminary performance test driven by the valve helium compressor is introduced, the test results are compared and analyzed, and the methods to further improve the performance are given. Key words: Four-valve pulse tube refrigerator "L" -type double orifice valve experimental study 1 Frontal pulse tube refrigerator is the use of a periodic pressure gas changes in a low thermal conductivity of the tube reciprocating oscillation, which Chiller with a large temperature gradient. Compared with other types of small cryogenic refrigerators, such as the G-M, stirling type refrigerators, the conventional cryogenic refrigerators are fundamentally solved because they have no moving parts in the low-temperature region of the conventional regenerative refrigerators Cold cavity vibration, wear and other outstanding problems, is expected to achieve long-life operation, and therefore in space technology, superconducting applications, communications, power and other high-tech fields have great potential applications. Since 1963, Guidant and Longsworth have proposed and developed a basic pulse tube refrigerator [1]. To date, pulse tube chillers have undergone many modifications, including small hole [2], double inlet [3] , Four-valve type [4], active gas tank type [5] and so on. Among them, the four-valve pulse tube refrigerator was introduced by Professor Matsubara Matsubara of Japan in 1993. The comparative test results show that this valve has a larger cooling capacity than the conventional small-bore pulse tube refrigerator [4]. Furthermore, the four-valve pulse tube refrigerator has a greater advantage in this respect for the moment in improving the performance of the refrigerator, mainly by adjusting the mass flow rate and the pressure wave phase of the hot end of the vessel, Potential as an efficient pulse tube cooler. Due to the large number of valves in four-valve pulse tube refrigerators, the current research focuses on single-stage studies. The researchers in Germany [6-7], Japan [4,8], and China [9] Machine are more research, research content is basically around to improve performance, stability analysis. At present, the best performance of the four-valve pulse tube refrigerator is obtained on the machine developed by Sumitomo Heavy Industries's Li Rui, etc. The minimum temperature of the tube cold head is 21.6K and the cooling capacity is 33.5W@80K [8]. In this paper, in order to further simplify the structure of the cold side of the refrigerator, an "L" type vascular structure is proposed. Two small orifice valves are used to control the inlet and exhaust volume of the hot side of the vessel respectively. Under the performance of the pilot study. 2 "L" type vascular structure and double orifice valve structure Compared with the usual four-valve pulse tube refrigerator, four-valve pulse tube refrigerator in this paper has two major characteristics: First, the use of "L" type pulse Tube structure to replace the usual "I" -type vessel structure, greatly simplifying the structure of the cold end of the vessel; the second is the hot end of the vessel double orifice valve structure to replace the usual single-valve structure, used to control the pulse Tube hot end of the exhaust gas mass flow rate. This can be better adjusted. (A) "I" type cold junction structure (b) "L" type cold junction structure Figure 1 Schematic diagram of two kinds of cold junction structure of a four-valve pulse tube refrigerator For the common single-stage parallel type pulse The cold tube is controlled by a straight, thin-walled stainless steel tube (referred to herein as "I" vessel), as shown in Figure 1 (a), with the cold end passing through the cold tube heat exchanger End connection tube, the regenerator cold-side heat exchanger and the regenerator cold junction, the cold end of the vessel along with the cold-side heat exchanger is called the cold head, and for the single-stage, four-valve pulse tube refrigerator in this context, A stainless steel tube of "L" type having an inner diameter of 19 mm and a wall thickness of 1.65 mm was used as a vessel, the angle of the middle elbow was 90 degrees (in which the length of the vertical portion was 148.4 mm and the length of the horizontal portion was 46 mm) (B), this directly connects the cold end of the regenerator to the cold end of the cold end heat exchanger, greatly simplifying the structure of the cryogenic end of the vessel. In other words, the original cold end connector becomes a vein As part of the tube, the two cold-side heat exchangers are combined. The typical four-valve pulse tube refrigerator has only one orifice valve at the hot end of the vessel for regulating the flow of intake and exhaust through the vessel. As shown in Figure 2 (a), the range of adjustment is limited. The four- Pulse tube refrigerator were arranged in the hot end of the two small orifice valves were used to regulate the hot end of the vessel into the exhaust flow, as shown in Figure 2 (b) below, the test results show that when the refrigerator reaches the minimum temperature The best opening of two small orifice valves is different, but also proved that the two small orifice valve can be more fully adjusted. (A) single orifice valve structure (b) double orifice valve structure Figure 2 four-valve pulse tube cryogenic vessel hot end of the two valve structures 3 test equipment test device system diagram shown in Figure 3, the compressor G-M refrigerator commonly used valve helium compressor rated input power of 5.5kW, it is through the pneumatic valve and orifice valve and the hot end of the refrigerator connected to adjust and control the valve timing pneumatic valve and refrigeration Machine working frequency. Cooler inner diameter of 40mm, wall thickness of 2mm, a length of 123mm stainless steel tube filled with 200 mesh bronze mesh. Figure 3 schematic diagram of the experimental device system Vessel and heat exchanger at the hot end of the heat exchanger are at room temperature, the hot end of the vessel heat exchanger using water cooling, regenerator hot end of the natural air-cooled heat exchanger, cold-side heat exchange The cold junction of the regenerator and the cold end of the vessel are directly connected, and the interior of the hot and cold side heat exchanger is filled with 20 mesh bronze wire mesh as the laminar flow element and the use of enhanced heat transfer. Gold and iron thermocouple thermometers are arranged at the cold head and the vascular elbow. Pressure sensors are arranged on the hot end of the blood vessel and the hot end of the cold regenerator, and the data are collected. Test system also includes vacuum system, data acquisition system. 4 Test Results and Analysis The initial test was carried out under the conditions of a compressor inflation pressure of 1.6 MPa and a working frequency of 2.5 Hz. After repeated tests, the minimum capacity of our new four-valve pulse tube refrigerator The temperature is 72K, Figure 4 shows the best aperture opening of the refrigerator cooling curve. After about 4 hours of operation (the usual four-valve pulse tube refrigerator also takes about 4 hours to reach the minimum temperature), the temperature of the refrigerator cold head tends to stabilize to 72K, the temperature of the vascular elbow at the basic The trend is stable at about 170K, the temperature of the vascular elbow is still relatively high, while the temperature difference between the two rises with the decrease of the temperature, finally showing a steady trend. The possible causes are analyzed as follows: firstly, There are two welding at the two ends of the elbow, which may result in the inner wall surface is not very smooth, and the welding place is relatively thick, resulting in a larger heat loss here, resulting in the elbow temperature is not easy to drop very low. Compared with the four-valve pulse tube refrigerator with "I" type of vascular structure, the cooling time is the same, but the lowest temperature reached by the cold head is relatively high. The reason for the analysis is mainly because the elbow and the straight tube are welded, Wall thickness has certain requirements, resulting in vascular wall thickness can not reach the ordinary vascular wall thickness (usually 0.5mm), thus resulting in a larger heat loss, the initial estimate of the heat loss here is 1.17W, The same temperature difference, the wall thickness of 0.5mm of the thermal conductivity of the straight vessel is only 0.365W. Figure 5 shows the effect of different orifice opening on the minimum load-free refrigeration temperature at the cryogenic head of the vessel. It can be clearly seen from the figure that the pulse tube refrigerator with a single orifice valve has the best small The same as the opening of the hole, there are two optimal openings in the refrigerator, the opening of O3 is 2.6 / 25 and the opening of O4 is 3.4 / 25. (For the small hole valve in this paper, the maximum opening Degree of 3 laps, each lap is divided into 25 cells), at this time, the temperature of the cold tube of the cryogenic refrigerator reaches a minimum of 72.1K. We found that the opening degree of the two small hole valves O3 and O4 at the optimal opening degree is different, which is also the structure of the single small hole valve, which shows that the adjustment capability of the single small hole valve is limited. The double Small hole valve structure can be better adjusted. Fig. 6 shows the change of the gas pressure at the hot side of the regenerator and the hot side of the regenerator when the refrigerator reaches the minimum temperature. The average pressure of the hot side of the vessel is slightly greater than the average pressure of the hot side of the regenerator due to the comparison of the resistance of the filler in the regenerator Large, the waveform in Figure 6 is far away from the normal square wave and is very similar to the sinusoidal waveform, indicating that there is greater flow resistance at the inlet of the cryogenic refrigerator. If a more suitable valve is used to reduce the airflow resistance, So that the inlet pressure wave closer to the square wave, so that the pressure at the highest point of time is longer, made of PV work increased, so that to improve the performance of the pulse tube cooler possible. Figure 7 shows the effect of different frequencies on the minimum temperature of the cold head of the refrigerator. It can be seen from the figure that the optimum operating frequency of the refrigerator is 2.5 Hz, and the lowest temperature of the cold head of the refrigerator is 72K at this time. Fig. 7. Effect of frequency on the minimum temperature of the refrigerator's cold head. 5. Conclusions and Prospects (1) An "L" vessel structure is proposed that greatly simplifies the cold junction structure of the vessel compared to the usual "I" vessel structure Increasing the symmetry of the structure, more importantly, the horizontal part of the vessel can be combined with the cold head to provide cold, greatly improving the utilization of cold energy. (2) The double-orifice valve structure is used in the hot end of the vessel. The experimental results show that the opening of the two small-aperture valves when the cold-head of the refrigerator reaches the minimum temperature shows that the double-orifice valve structure is smaller than the single- Valve structure can be better adjusted. (3) The minimum temperature 72K which the refrigerator in this article can reach is not very ideal. The reason for this analysis is that the restriction of the wall thickness at both ends of the elbow results in that the wall thickness of our "L" -type vessel can not be To ordinary "I" -type vessels so thin, resulting in greater heat loss. So further how to improve the welding means to reduce the "L" vessel wall thickness will be our next major work. At present, copper metal foam materials have been used to replace the screen material on the heat exchanger to enhance heat transfer experiments.
A transmission Oil Cooler is often considered essential in high-strain situations because a transmission's lubricating fluid heats up with each gear change. While not crucial for highway driving when vehicles more or less stay within a few gears, transmission coolers can markedly improve the performance and longevity of transmissions that are subjected to a great deal of stress. Overheated transmission oil can lead to slower gear shifts, worn seals, lower mileage, and, ultimately, premature failure.
Even though the main job is to cool and lubricate the engine, this part can also act as an important coolant for a number of other parts. A motor's bottom end, which includes parts such as the crankshaft, bearings, camshaft, rods, and pistons, is also cooled only by engine oil, for instance, and this cooling can impact overall performance just as much as it could in the engine itself.
As an important type of engineer oil cooler, stacked-plate designs, force oil through a series of metal plates. Heat dissipates as air moves across the plates, and the oil cools faster when it has greater surface area and is shallower, too. The oil cooler can improve the engineer`s performance and longevity, and also can help lubricate the gears of a vehicle`s transmission system.
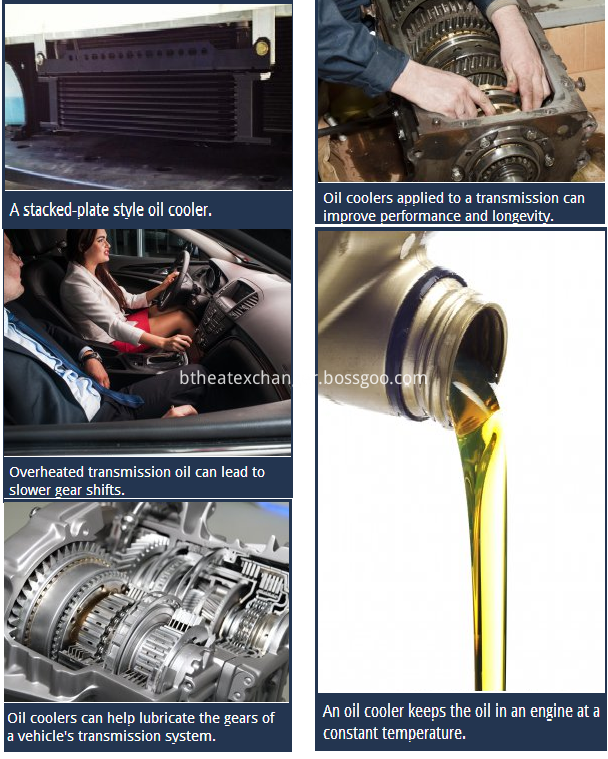
Stacked Plate Oil Cooler
Engine Oil Cooler,Stacked Plate Oil Cooler,Car Oil Cooler,Transmission Oil Cooler
Wuxi Better Technology Co., Ltd , https://www.btheatexchanger.com