At JST Industry, we use the latest machining technology with a wide range of capabilities to meet your demands. Our manufacturing facilities include 3-5 axis milling, lathes, grinding, etc, and state of the art metrology. With these machines, we produce complex parts in the most efficient and accurate way. Our manufacturing capabilities allow us to develop your part from prototype to mass production for the most precise of jobs.Â
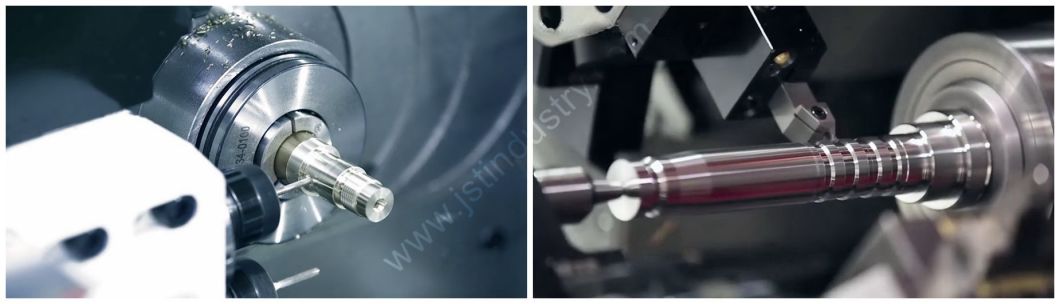
Â
Processing Method | CNC Milling, CNC Turning, Turning-Milling Machining, Micro Machining, Grinding, Boring, Tapping. |
Material | Stainless Steel, Alloy Steel, Carbon Steel, Free-cutting Steel, Brass, Copper, Aluminum, POM, PTFE. |
Finish Treatment | Polishing, Sand Blasting, Anodizing, Zinc Plating, Nickel Plating, Blackening, QPQ, Painting, etc.. |
Tech. Standard | ANSI, ASTM, DIN, JIS, BS, GB, ISO, etc.. |
Application | Medical, Aerospace, Millitary, Instrument, Optics, Food Equipment, AUTO Parts, Furniture, etc.. |
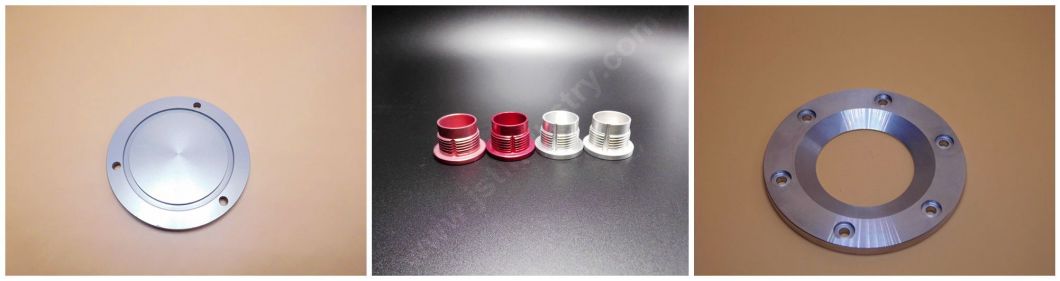
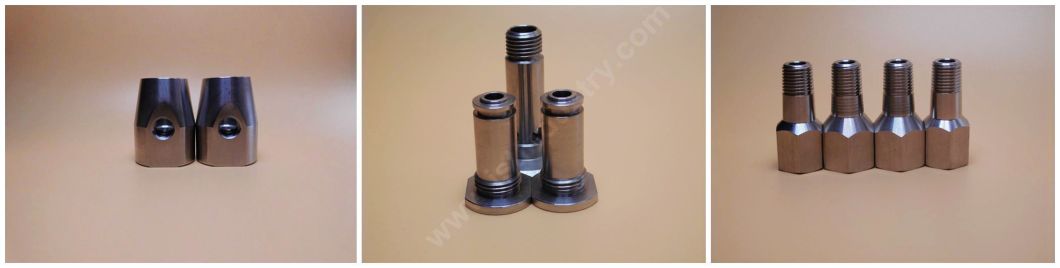
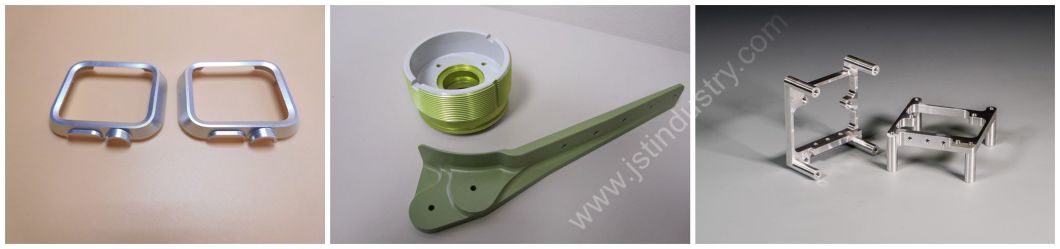
Precision Machining is the most important sector in JST Industry, we have been a trusted manufacturing supplier in this field for over 15 years. We have built an impeccable reputation on quality, customer service and utilizing state-of-the-art equipment. Our expertise has made us the Best in Quality and Innovation.
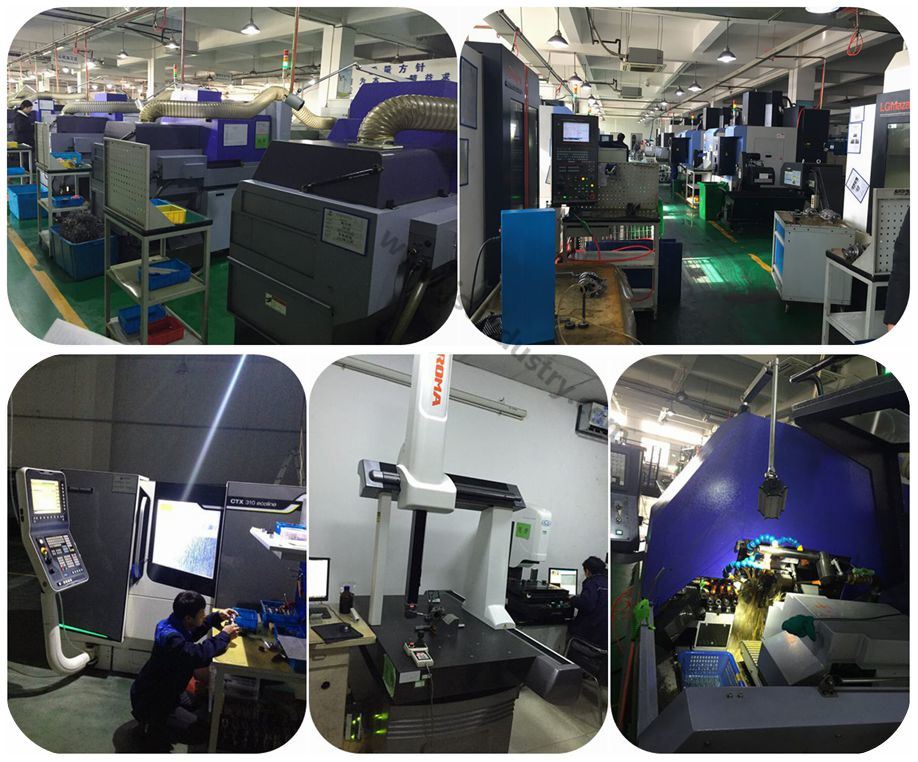
Machining Facilities
 Equipment Description |   Workpiece Dimensions | Processing Accuracy |  Quantities |  Brand |
3-axis machining center | Max. 1000 x 1200mm | +/-0.01mm | 6 | DMG |
4-axis machining center | Max. 1000 x 1500mm | +/-0.01mm | 4 | DMG |
5-axis machining center | Max. 1000 x 1500mm | +/-0.01mm | 2 | DMG |
CNC lathe | Max. diameter 100mm | +/-0.01mm | 20 | SMTCL |
General lathe | Max. diameter 500mm | +/-0.05mm | 2 | SMTCL |
Turning-Milling Machine | Max. diameter 100mm | +/-0.01mm | 6 | DMG |
Longitudinal lathe | Max. diameter 30mm | +/-0.01mm | 6 | TSUGAMI |
Automatic lathe | Max. diameter 20mm | +/-0.02mm | 30 | TY |
CNC Swiss Lathe | Max. diameter 20mm | +/-0.01mm | 6 | TSUGAMI |
Other assist equipments include:
Milling machine, Drilling Machine, Centerless Grinding machine, External Cylindrical Grinding machine, etc.
Inspection equipment:
Vernier Caliper, Micrometer, Height Gage, Hardness Tester, Two-dimensional image measuring instrument, TESA Micro-Hite
300, Mitutoyo surface Roughness Tester, Mitutoyo CMM and Ultrasonic Cleaner.
FAQ
Q1: Are you a trading company or a manufacturer?
Manufacturer.
Â
Normally, the samples delivery is 10-15 days and the lead time for the official order is 30-45 days.
Â
Normally, it will take 2-3 days.
Â
Yes, the samples will be free if  the cost is not too high.
Â
America, Canada, Europe, Australia and New Zealand.
Â
Yes, we have over 10 years exporting experience and 95% of our products were exported to overseas market. We specialized in the high quality OEM parts, we are familiar with the standard of ANSI, DIN, ISO, BS, JIS, etc..
Â
Yes, we have been appointed as the supplier of Parker(USA) Â since 2012. "Supply the top quality precision machined parts" is our management philosophy, ON TIME and EVERYTIME.
CNC punching and shearing equipment for the processing of angles studied for small and medium size steel construction companies. These lines provide flexibility and simple use, and are characterized by an innovative infeed roller conveyor system allowing high precision with minimum loss of material.
Advantages:
- Versatile solution: each model can be configured according to the most diverse production lots and to customer requirement with an affordable investment.
- Compact frame for easy installation and reduced overall size.
- Remote diagnosis is possible through a network connection that allows our service team to perform routine checks
The linear tool carrier (y-axis) has several stations that hold the punching tools and one cutting tool. Especially for flexibility and efficient processing are setup times a crucial cost factor. Downtimes should be reduced to a minimum. Therefore, recent tool systems are designed for fast and convenient change of punches and dies. They are equipped with a special plug-in system for a quick and easy change of tools.
There is no need to screw anything together. The punch and die plate are adjusted to each other automatically Punches and dies can be changed rapidly meaning less machine downtime
Angle punching round hole and s-lot hole samples
The Punching Unit:
This
unit is consists of three pieces of machine body, two hydraulic pressure
punching cylinders, four die bases with upper and lower dies, and two sets of
servo systems for controlling stadia adjustment. This unit can be installed three
different standards punches on each side. Every punch matches with one gas
cylinder. The gas cylinder piston pole links a padding block, which installed
between punch poles and oil cylinder press head. It automatic chooses punch,
namely choose relevant gas cylinder to drive relevant padding block according
to the order of computer. The position of stadia is located by servo motor,
which drives ball screw to drive die base move up and down, thus to achieve the
requirement of stadia position. It can punch many rows and different diameters
holes on two wings of angle steel.
The Marking Unit:
New design for type marking unit, more stable and longer life
This
unit consists of fix lathe bed, movable lathe bed, hydraulic pressure head,
four positions oil cylinders (can change four positions for character boxes)
and adjusting device. According to the order of computer, to mark on places the
drawings require. For making the mark clear and endurable, and avoiding the
angle steel abrade character heads, it adds oil cylinder of movable lathe bed
uplift and falling. For satisfying the processing scope, it adds manual
adjustment setup, which can change the position of characters to adapt
different standards angle steel.
The Shearing Unit:
This unit consists of frame
machine body, hydraulic pressure dynamic cylinder, upper blade setup, lower blade
setup, and front bracket tank etc. The front bracket tank avoids angle steel to
strike lower blade. The lower blade setup can adjust the clearance according to
angle steel thickness to ensure the cutting quality. It cuts different
standards of angle steel, according to the order of computer.
The Feeding Conveyors:
Double linear guide and detection rack for total
feeding conveyor ensure better accuracy and machine stability. Linear guide
from Taiwan HIWIN.
The NC Feeding Carriage:
Newest NC carriage, linear guide drive, accuracy
and stability much better!
NC carriage linear guide cushion, pneumatic lift
Work Table And Overturning Rack:
Overturn
rack for loading material automatically
Angle Punching Marking Shearing Line
Angle Punching Marking Shearing Line,Angle Connecting Plate Punching,Punching Shearing And Marking Line,CNC Angle Production Line
Shandong Sunrise CNC Machine Co., Ltd , https://www.scmcnc.com