Discover the World of Electrical Enclosure Manufacturers
- Why electrical enclosures are essential across different industries.
- The full manufacturing process, from design to final testing.
- How manufacturers ensure quality, compliance, and customer satisfaction.
Are you interested in understanding how electrical enclosures are made by leading manufacturers? These enclosures play a crucial role in protecting sensitive electrical components from environmental damage, ensuring safety, and maintaining operational efficiency. From industrial settings to commercial applications, they are used in a wide range of sectors. Companies like Atlas Manufacturing, with over 60 years of experience, specialize in precision sheet metal fabrication, offering end-to-end solutions that cater to a variety of needs.
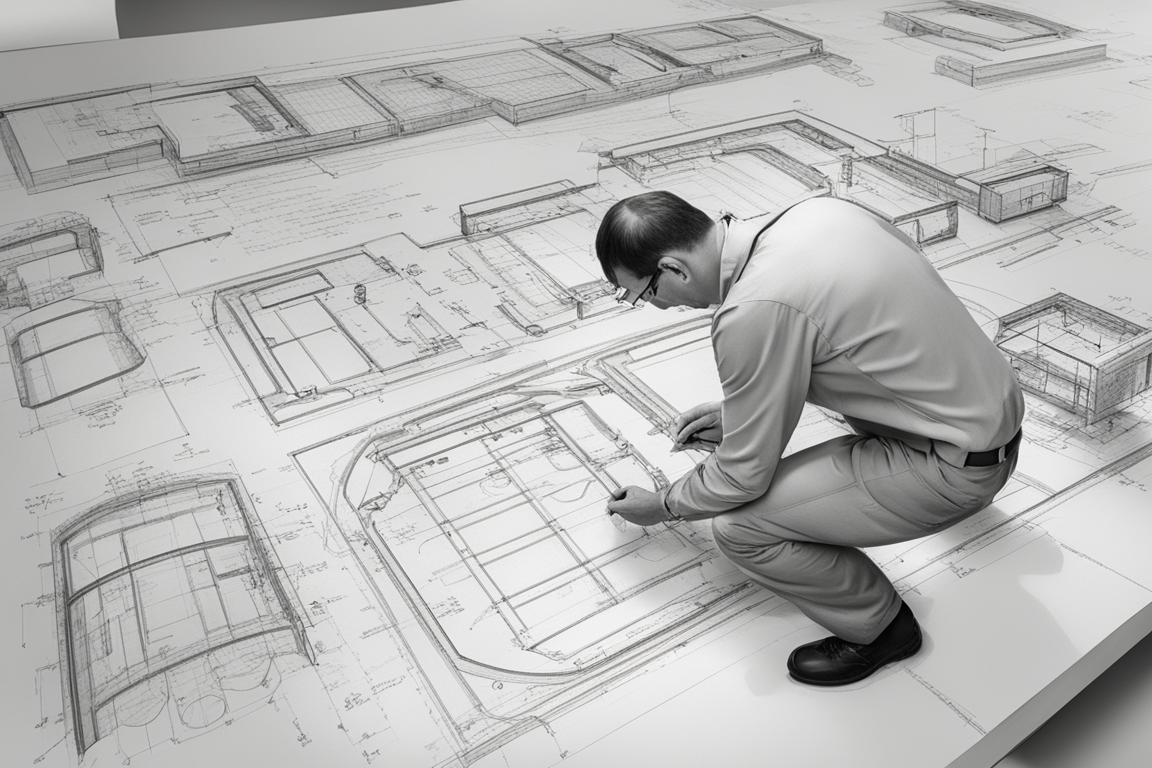
Design and Specification Phase
The first step in the manufacturing process is the design and specification phase. Engineers and designers work closely with clients to develop detailed blueprints that meet specific requirements. Factors such as size, material type, environmental conditions, and industry standards are all considered to ensure the enclosure is both functional and compliant.
Material Selection
Selecting the right material is vital for the performance and longevity of an electrical enclosure. Common options include carbon steel, stainless steel, aluminum, and various plastics. Each material has unique properties—like corrosion resistance, weight, and conductivity—that influence its suitability for different applications. Manufacturers help customers choose the best option based on their needs.
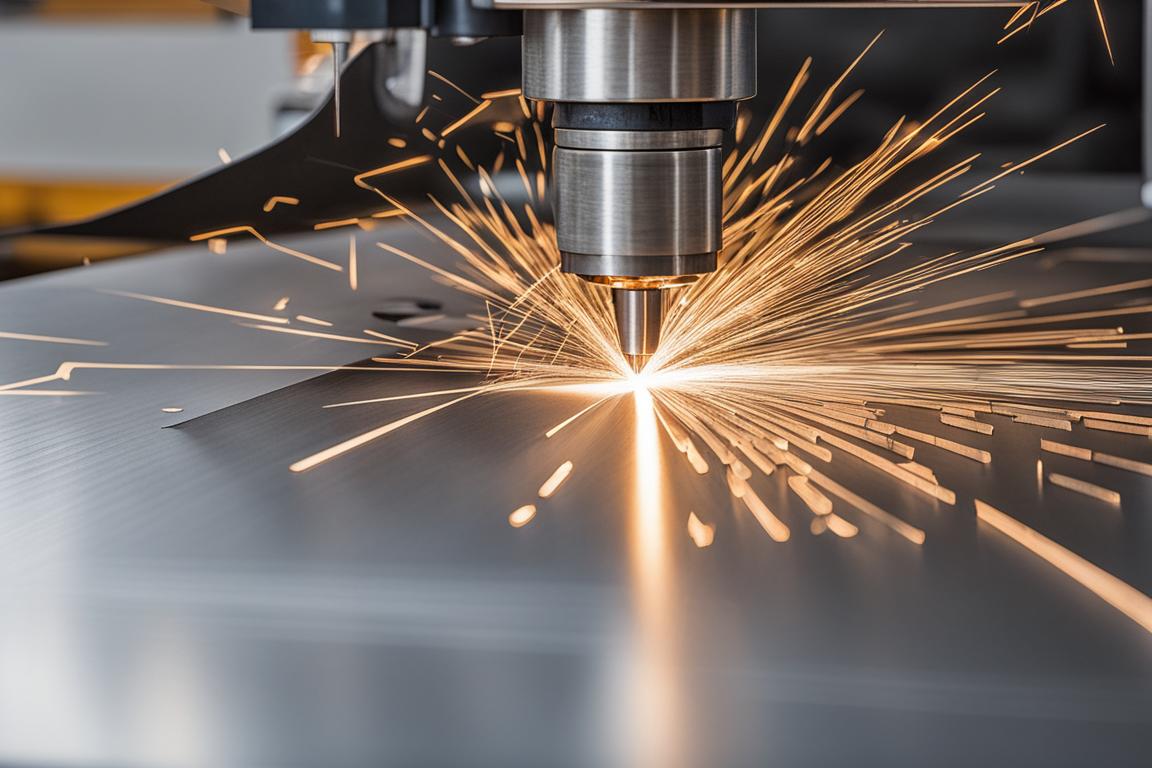
Cutting and Blanking
Once materials are chosen, advanced cutting tools like laser cutters and punches shape them into precise sizes. This stage is critical for ensuring that all parts fit together correctly during assembly. Accuracy at this point ensures the final product is both functional and visually appealing.
Bending and Forming
Metal sheets are then bent into three-dimensional shapes using press brakes. Skilled operators ensure that each bend meets exact specifications, preserving the structural integrity of the enclosure. Proper bending is essential for seamless assembly and long-term durability.
Aspect | Description |
---|---|
Equipment | Press brakes are used for accurate bending operations. |
Precision | Ensuring accurate bends to match design plans. |
Skilled Labor | Trained personnel operate the machinery effectively. |
Structural Integrity | Preserving the strength and stability of the enclosure. |
Functionality | Allowing for smooth component assembly and use. |
The Importance of Precision in Bending
Press brakes are key tools in creating high-quality electrical enclosures. Their ability to make precise bends ensures that the final product meets all design and functional requirements. This attention to detail is what sets top manufacturers apart.
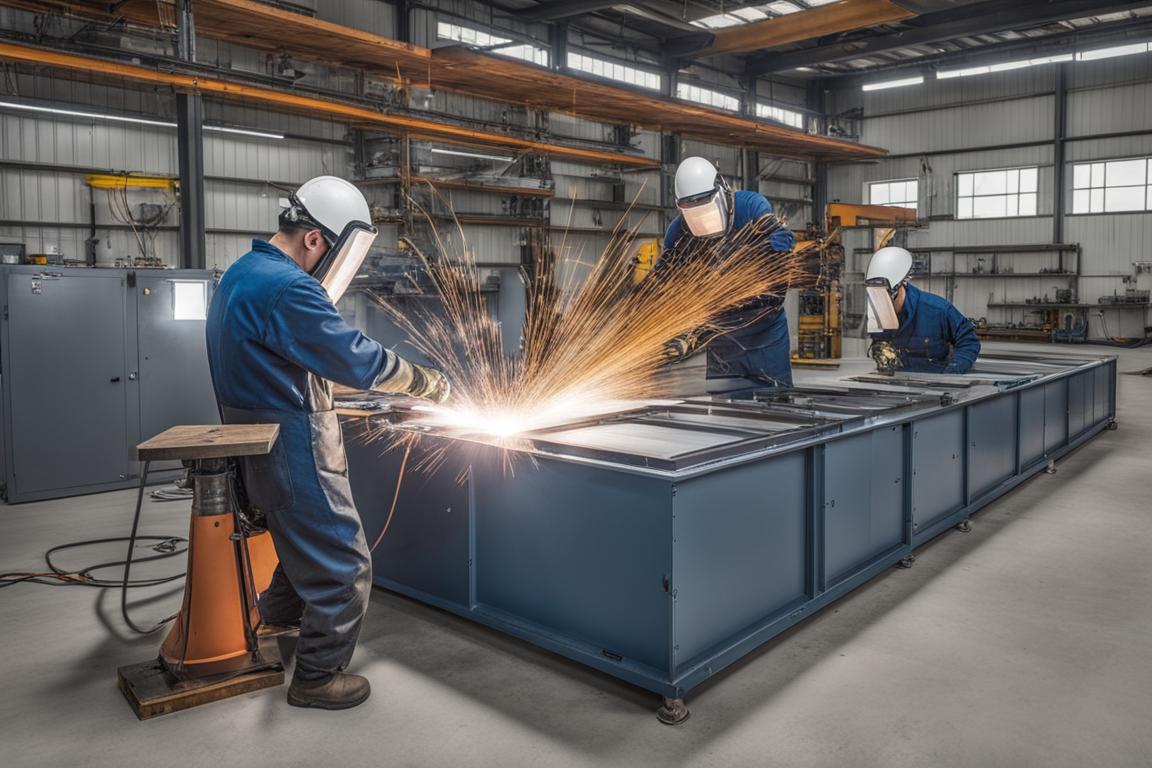
Welding and Assembly
After bending, the next step is welding, where components are joined using techniques like MIG or TIG welding. This process strengthens the structure and ensures the enclosure can withstand harsh conditions. Additional assembly steps include attaching doors, hinges, gaskets, and mounting brackets to complete the unit.
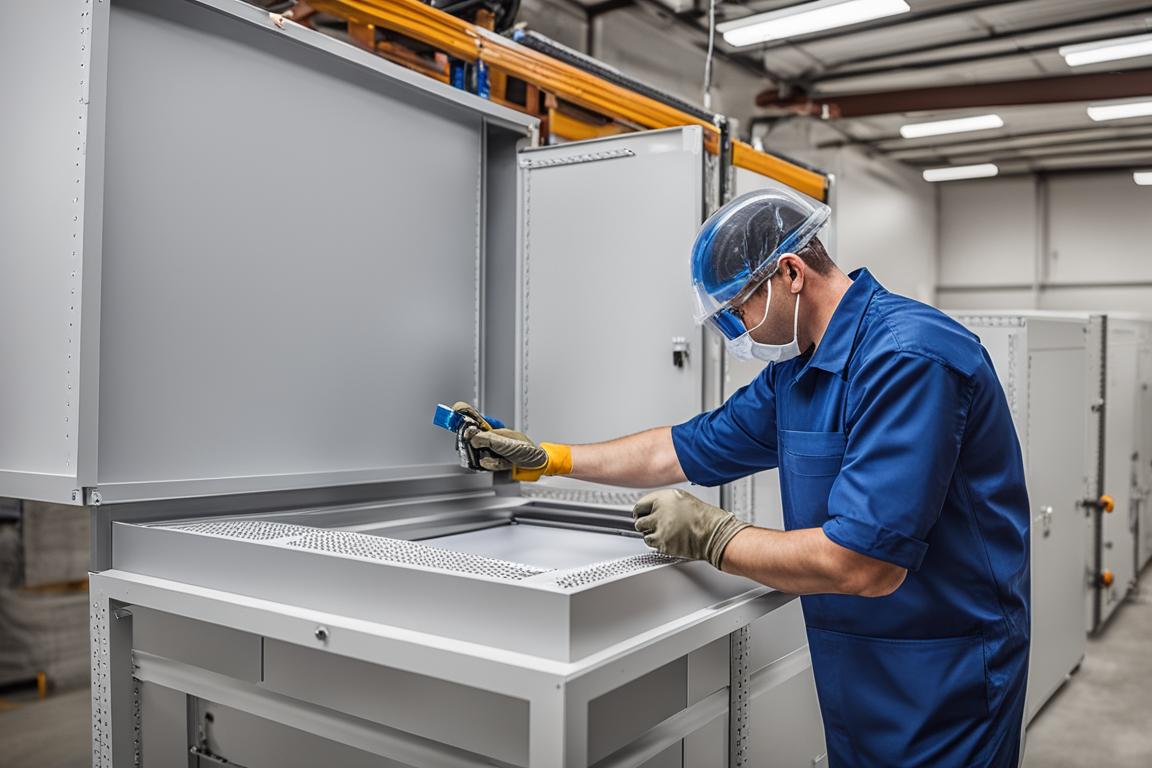
Finishing and Coating
Enclosures undergo finishing processes such as powder coating, painting, or anodizing to enhance durability and appearance. These finishes protect against corrosion, UV exposure, and wear, making the enclosures suitable for both indoor and outdoor use.
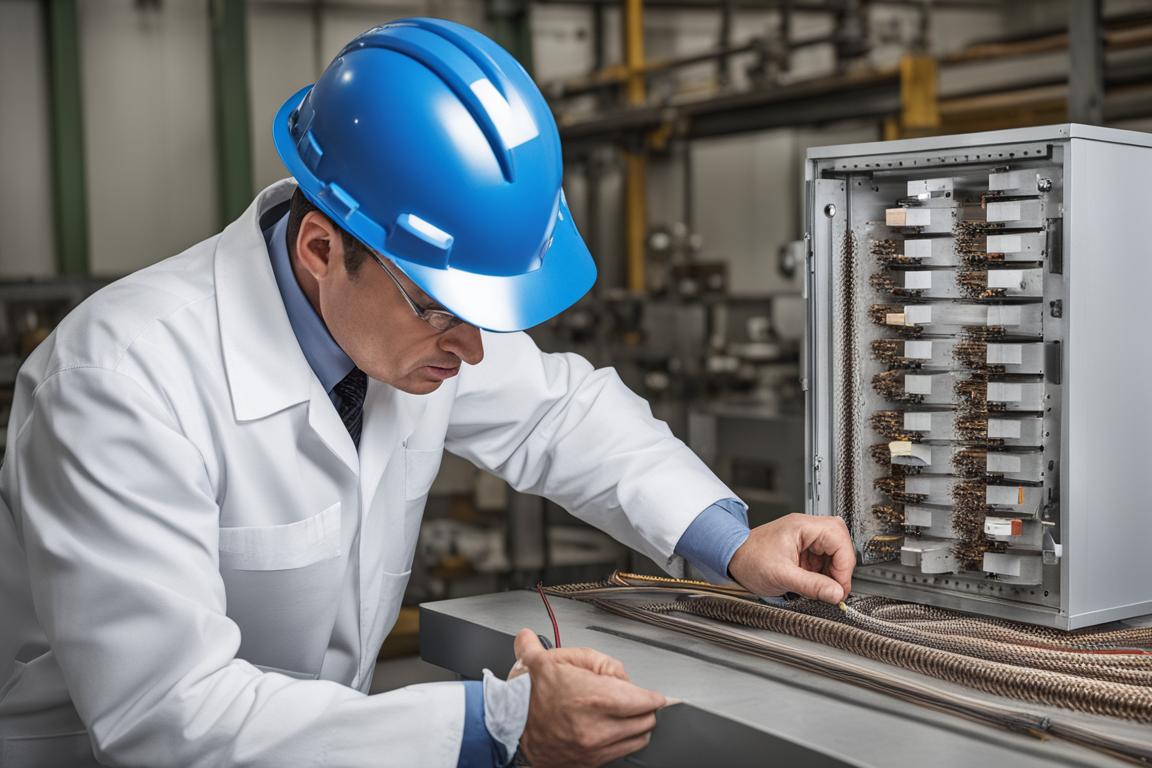
Quality Control and Testing
Throughout the manufacturing process, strict quality checks are performed to ensure every part meets the required standards. Testing includes pressure tests, electrical conductivity checks, and visual inspections to guarantee the enclosure is safe and reliable.
Certifications and Compliance
Manufacturers often obtain certifications like NEMA, IP, UL, CE, and RoHS to prove their products meet global safety and quality standards. These certifications not only build trust with customers but also ensure that the enclosures are suitable for international markets.
Packaging and Shipping
Proper packaging is essential to protect enclosures during transit. Manufacturers use secure methods to prevent damage, ensuring the product arrives in perfect condition. Efficient logistics support helps streamline delivery and reduce lead times.
Customer Support and After-Sales Service
Leading manufacturers provide ongoing support, including technical assistance, customization, and maintenance services. This ensures that customers receive long-term value and satisfaction from their purchases.
Conclusion
In summary, the manufacturing of electrical enclosures involves a complex and well-structured process that combines engineering, precision, and quality assurance. Companies like Atlas Manufacturing excel in delivering durable, safe, and customized enclosures that meet the highest industry standards. Whether for industrial, commercial, or residential use, these enclosures are essential for protecting valuable electrical equipment.
If you want to learn more about how electrical enclosures are made, feel free to reach out to us. We're here to help you understand the process and find the best solution for your needs.
Frequently Asked Questions
Q. Who are some top electrical enclosure manufacturers in precision sheet metal fabrication?
A. Some of the top names include Hoffman, Rittal, and Hammond.
Q. What materials are commonly used for electrical enclosures?
A. Common materials include stainless steel, aluminum, and galvanized steel.
Q. How can I ensure my enclosure meets my specifications?
A. Provide detailed drawings and specifications to the manufacturer for custom production.
Q. Can I get a custom design if it's not listed?
A. Yes, many manufacturers offer custom design services to suit your specific needs.
Q. How long does it take to produce a custom order?
A. Production time typically ranges from 2 to 6 weeks, depending on complexity.
Q. What finish options are available?
A. Options include powder coating, painting, and plating to meet your preferences.
{"@context":"https://schema.org","@type":"FAQPage","mainEntity":[{"@type": "Question", "name": "Who are some top electrical enclosure manufacturers in precision sheet metal fabrication?", "acceptedAnswer": {"@type": "Answer", "text": "Some top manufacturers include Hoffman, Rittal, and Hammond."}}, {"@type": "Question", "name": "What materials are commonly used by precision sheet metal manufacturers for electrical enclosures?", "acceptedAnswer": {"@type": "Answer", "text": "Common materials used include stainless steel, aluminum, and galvanized steel."}}, {"@type": "Question", "name": "How can I ensure the electrical enclosure meets my specifications?", "acceptedAnswer": {"@type": "Answer", "text": "You can provide detailed drawings and specifications to the manufacturer for custom fabrication."}}, {"@type": "Question", "name": "What if I need a custom design that is not listed by the manufacturer?", "acceptedAnswer": {"@type": "Answer", "text": "Many manufacturers offer custom design services to meet specific requirements."}}, {"@type": "Question", "name": "How long does it typically take for electrical enclosure manufacturers to produce a custom order?", "acceptedAnswer": {"@type": "Answer", "text": "The production time varies but usually ranges from 2 to 6 weeks for custom orders."}}, {"@type": "Question", "name": "What if I have specific requirements for the finish of the electrical enclosure?", "acceptedAnswer": {"@type": "Answer", "text": "Many manufacturers offer a variety of finishes including powder coating, painting, and plating to meet specific needs."}}]}Peroxide,peroxid,Organic peroxide,chemical compound
Jiangyin Thousands Chemicals Co. , https://www.wqhxcomposite.com